東レとホンダが新たに挑むガラス繊維配合ナイロン6のリサイクル
(前編)
東レ株式会社(以下「東レ」)は、株式会社本田技術研究所(以下「ホンダ」)と、使用済みの自動車から回収するガラス繊維配合ナイロン6樹脂の部品を亜臨界水(高温・高圧状態の水)で解重合し、原料モノマー(カプロラクタム)に再生する、ケミカルリサイクル技術に関する共同開発契約を締結し、技術実証を開始しました。本件は環境省令和5年度脱炭素型循環経済システム構築促進事業(うち、プラスチック等資源循環システム構築実証事業)(補助)に採択されております。
ナイロン6のケミカルリサイクルスキームを構築することで、資源循環型社会の実現に貢献することを目指す、この共創事例について、東レとホンダ、両社のキーパーソンにインタビューを行いました。
前編では共創が始まった経緯、技術開発の要点や目的、今後の展開などについて話を聞きました。
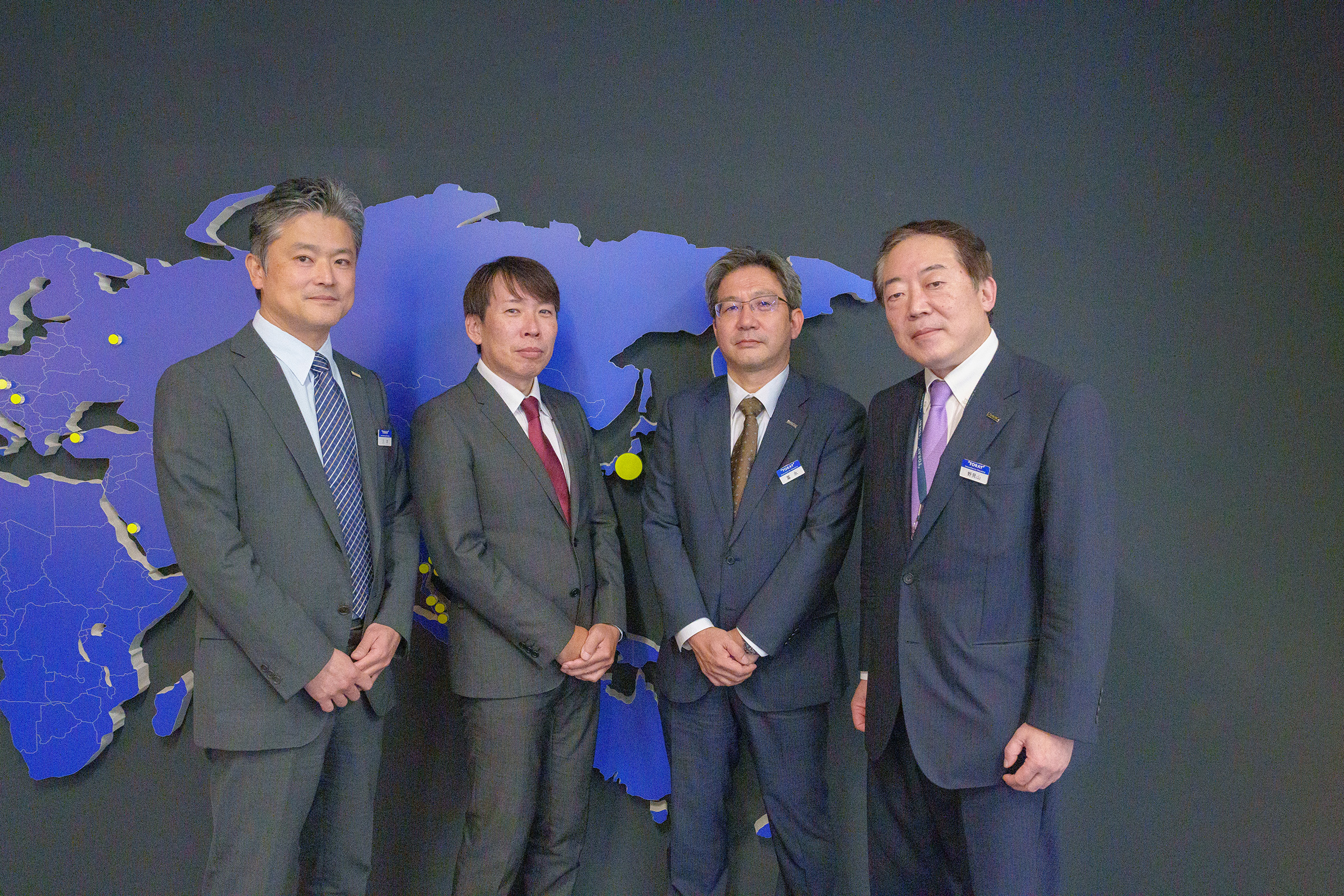
自動車部品のナイロン6を対象に、ケミカルリサイクル技術を共同開発
ー 自己紹介を兼ねて、この共創事例における役割についてお聞かせください。
平脇聡志氏(株式会社本田技術研究所 先進技術研究所 材料・プロセス領域 チーフエンジニア/以下、平脇氏)
本田技術研究所に2019年から先進技術研究所という部署ができたのですが、私はそこでサーキュラーエコノミー、資源循環の取り組みを行っています。
富永剛(東レ株式会社 研究本部 化成品研究所ケミカル研究室長/以下、富永)
私は、名古屋事業所にある化成品研究所ケミカル研究室におります。ホンダさんとの共同開発において、東レ側の開発の統括をしています。
野見山浩一(東レ株式会社 樹脂・ケミカル事業本部 樹脂・ケミカルサステナビリティ・イノベーション推進室長/以下、野見山)
私は、樹脂・ケミカルサステナビリティ・イノベーション推進室で、環境配慮型樹脂の事業企画を行う部署におります。リサイクルの原料・原資の調達も担っています。
三本陽明(東レ株式会社 自動車材料事業部長/以下、三本)
私は自動車材料事業部におり、自動車用途むけのエンジニアリングプラスチックのマーケティングセールスを担当しています。今回の共創では、リサイクルされた製品を取引先に提供する立場です。
ー ホンダが回収・分別・前処理を担当しているそうですが、具体的には何を回収し、どのように分別や前処理を行っているのですか?
(平脇氏)
使用済みの自動車から回収可能な、大物のプラスチック樹脂部品をターゲットにしています。その中で今回はインテークマニホールドという、ナイロン6で出来て いる部品が対象です。インテークマニホールドはホンダだけでなく、他のOEMを含め、世界中の自動車メーカーがナイロン6という材料を使っているのですが、それを原資として集めてリサイクルしていきます。
前処理としては、部品のままだと大きすぎて、モノマーという原料に戻す設備に入れられないので、粉砕して小さくします。その後に、金属やゴムといった異物を除去します。さらに、より細かい1cm角未満のサイズに粉砕することによりロジコストも抑制できます。
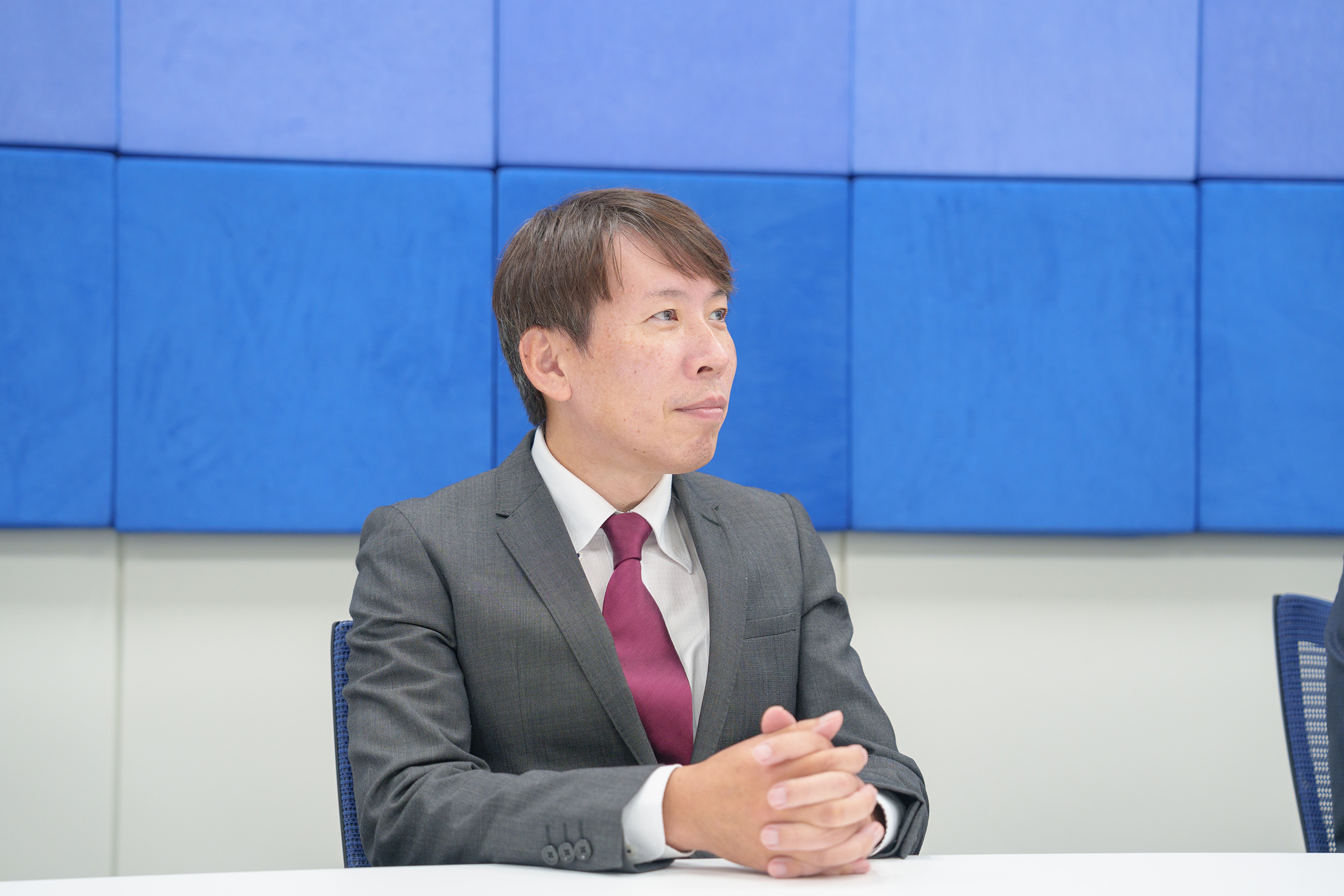
ー 東レが担っている技術開発についてお聞かせください。
(富永)
ナイロン6部品のケミカルリサイクルに亜臨界水という水を使うのですが、亜臨界水による樹脂の分解自体は古くから知られてはいるものの、まだ社会実装していない技術です。亜臨界水とは、一定レベルの高温・高圧状態の水のことで、水だけで分解する強い力を持っています。この特性を利用して、ポリマーであるナイロン樹脂をモノマーの状態に分解する、解重合技術に取り組んでいます。今の自動車に使われている部品は、ナイロン6樹脂に強化剤としてガラス繊維を大量に入れるなど、色々な添加剤が入っています。ナイロン6を解重合するのと同時にガラス繊維等をいかに分離していくか、というのが我々が担う技術開発であり、今回のホンダさんとの取り組みのポイントです。
ほぼナイロン6だけで出来ている漁網などは、社会実装されている既存のケミカルリサイクル技術で再び漁網に戻せますが、その技術は今回のように色々な添加物が混ざっている自動車部品に適用するのが難しいのです。
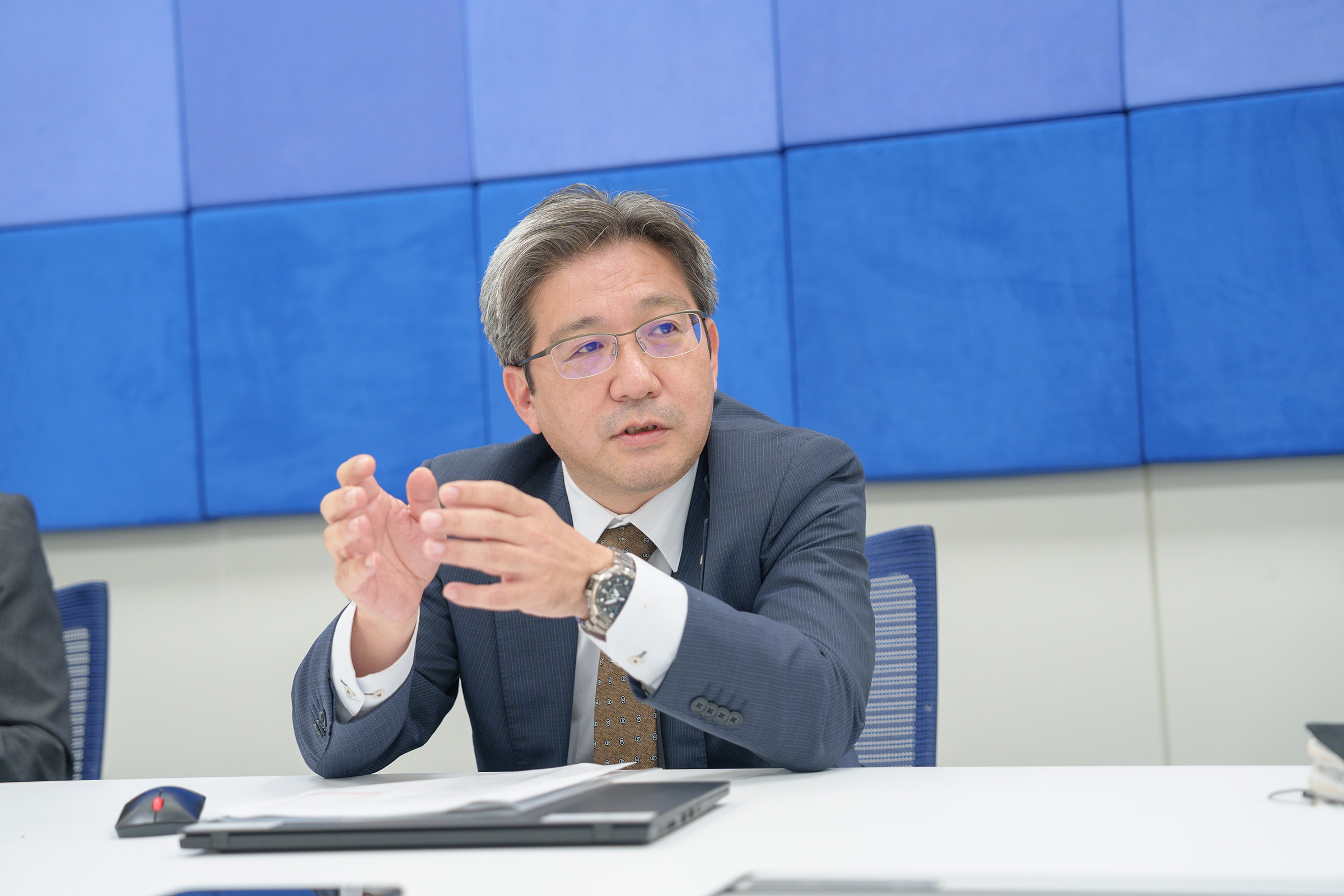
パートナーとして「リサイクルの環」を循環させる
ー この実証実験における両社の役割は?
(富永)
回収・分別のフェーズでは、ナイロン6部品がどういった状態なのかをホンダさんに聞きながら我々も一緒にやりますし、ガラス繊維を分離するところもお互いに知恵を出し合いながら進めています。モノマーからポリマーを重合するところは弊社の既存のインフラを活用し、ナイロン6にして、ガラス繊維を再び混ぜて、コンパウンドにしていくのですが、それを自動車部品として、どこにどのように使っていくかというところはホンダさんに委ねます。
とはいえリサイクルのプロセスは循環しているので、ここはホンダさん、ここは東レ、と線引きできるものでもありません。その環のなかでホンダさんと一緒に開発を行っており、だからこそ今回の共同開発に繋がったといえます。
(平脇氏)
ホンダ側も同じ認識です。これまでの取引のように役割分担を分けるのではなく、お互いが、共に歩んでいく完全に対等なパートナーなのです。
(富永)
自動車メーカーとしてホンダさんが強いところと、化学・高分子メーカーとして東レが強いところがそれぞれあるので、それぞれの得意領域を活かしながら実証実験を進めています。
【ケミカルリサイクルの技術実証スキーム】
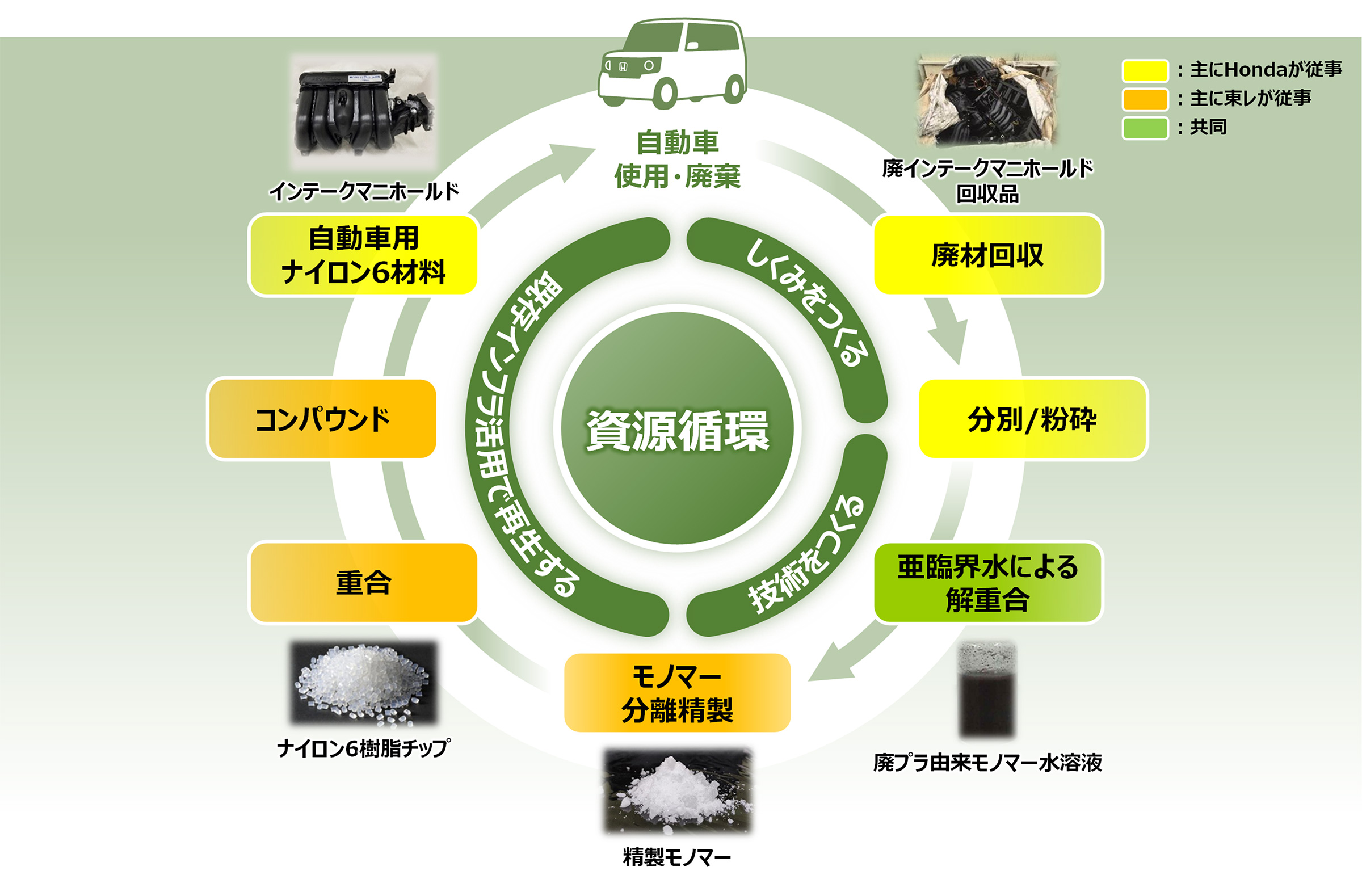
ー 実証実験を着手するまでの経緯は?
(平脇氏)
自動車部品であるナイロンの廃材をリサイクルするために樹脂の原料であるモノマーに戻すのですが、ホンダは素材メーカーではないため自己実証が出来ません。実証するためには樹脂メーカーさんと一緒に取り組む必要があり、そこで私たちから東レさんにお声がけさせてもらいました。
(富永)
東レは樹脂の原料をモノマーにするだけでなく、樹脂そのものを再利用するマテリアルリサイクルも行っています。ナイロン以外でも、たとえばPETフィルムや繊維を同様にモノマーに戻して重合し、PETに戻すなどの取り組みは以前から色々とやっており、それらのリサイクルに関する知見はありました。
ー 東レのサステナビリティ・イノベーションにおいてリサイクル技術の開発はどのように進めているのですか?
(野見山)
具体的なリサイクルスキームを構築することも業務範囲です。既存使用されているバージン材並みの物性に回復させることを目標に、まず最適な原資の選択をします。その上で原資の前処理をはじめ、各種加工工程を通ることでの素材に与える影響を確かめて、樹脂の性能、品質を確立していきます。品質の良い原資調達が重要であると考えており、このため、解体業者を訪ねたり、海外から調達を行う等、非常に幅広い活動になっています。
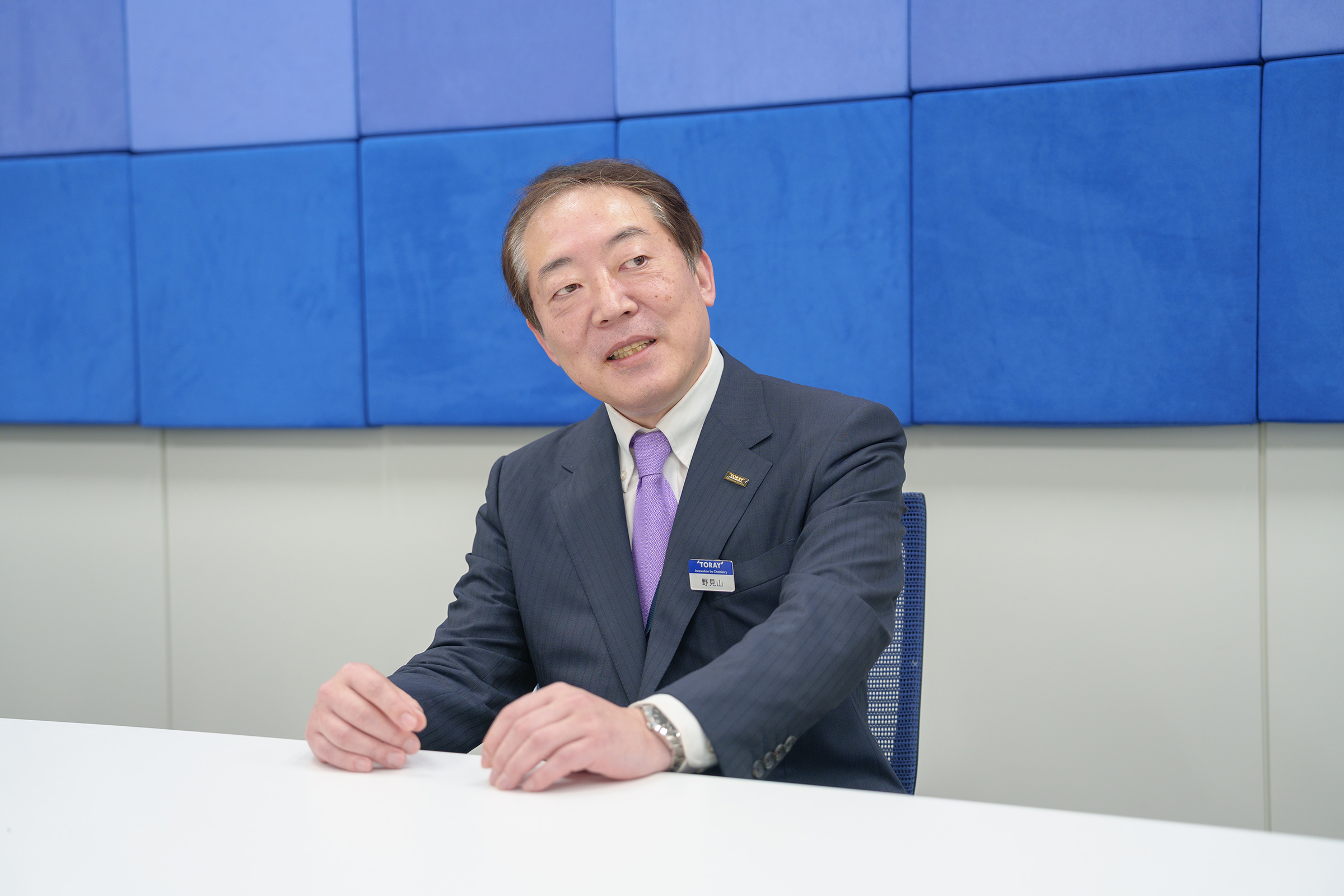
ー マーケティングの観点から、市場における期待感や要請をどのように感じておられますか?
(三本)
リサイクル材の活用や、どのような原資をどういった部品に適用していくかについては、各社で検討が始まっています。サーキュラーエコノミーの取り組みは今後ますます過熱していくと見ています。
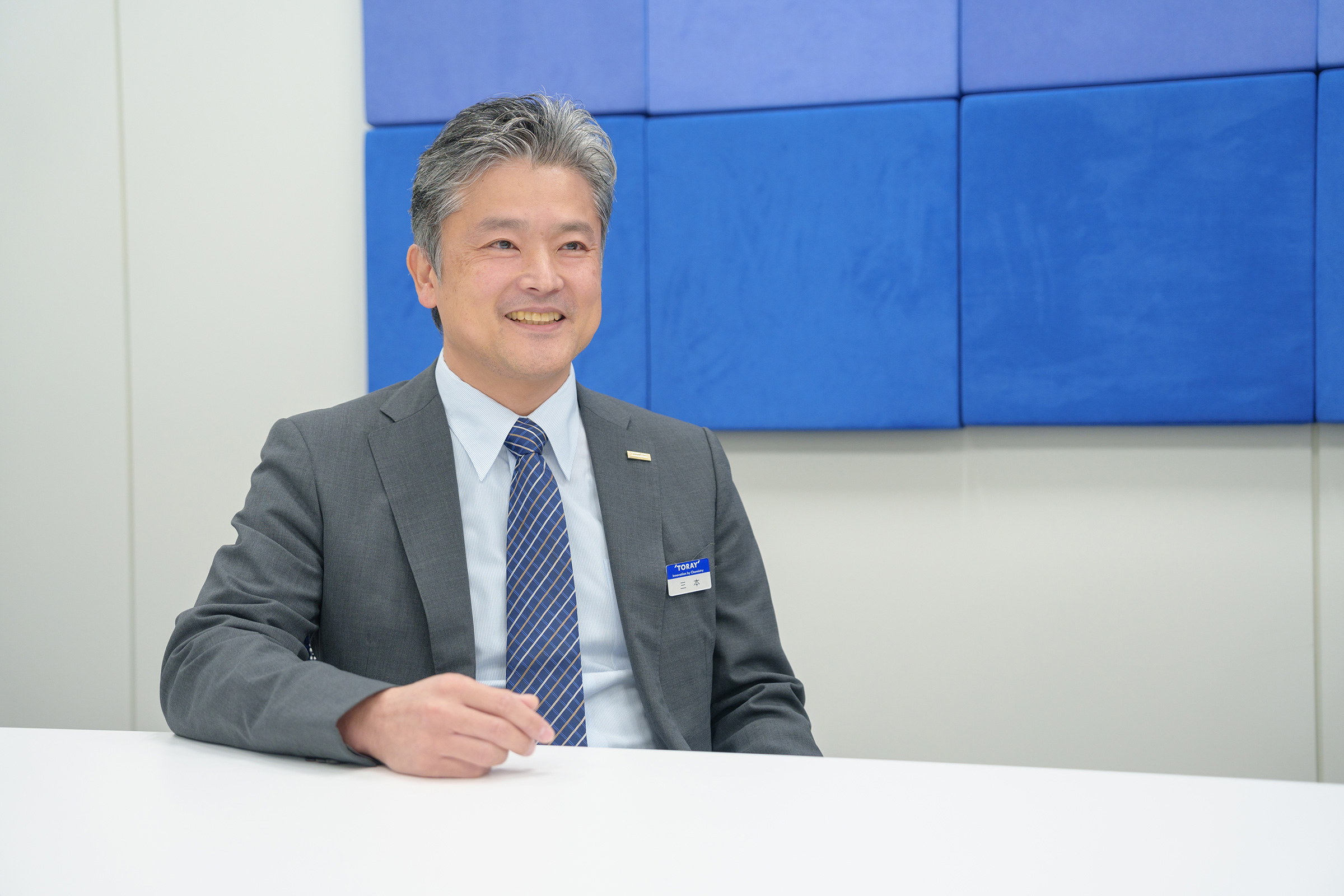
亜臨界水でより効率的なリサイクルを実現していく
ー 今回の共同開発では「亜臨界水でリサイクルする」ことが重要なのですね。
(野見山)
当社は従来よりケミカルリサイクルを進めていました。また、亜臨界水についても公知の技術でしたので、その知見はありましたが、開発するのであれば亜臨界水で進めたいというホンダさんの意向を受けて、すぐに試作機を導入して評価を進め、今般、亜臨界水を用いて実証実験を行う運びとなりました。
(富永)
自動車部品をリサイクルする場合には、色々な添加剤やガラス繊維が混ざっている状態から、どのようにリサイクルするのかを考えなければなりません。しかも、亜臨界水は高温・高圧の水です。その状態にするにはエネルギーを使うので、却って環境に負荷をかけないか? との点も考慮する必要がありました。
けれども、実際にラボで試してみると極めて短時間で処理ができ、環境負荷低減と両立できる可能性を見出しています。さらに、有機溶媒を用いず水で出来るのならば面白い技術になりそうだと我々も可能性を感じました。
また、東レはナイロン6の原料となるモノマー自体も製造しており、不純物をなくす技術があります。それを活用すれば、使用済みで汚れているリサイクル原資をきれいなモノマーにすることも出来ます。どういった原料にどのような不純物が入っているかについて、ホンダさんと一緒にやることで僕らも詳しく分かりますし、より効率的な精製の方法を追求することが出来るのです。
この技術を実証できれば、より多くのナイロン6がリサイクル可能になるはずなので、最初の難しい一歩を、ぜひホンダさんと共に挑戦したいと思いました。
(平脇氏)
今回なぜ亜臨界水でやるのかですが、まず、水を使うためにクリーンだということ。そして、他と比べて1/5と、非常にハイスピードで処理できることがその理由です。さらに、なぜ東レさんにお声がけしたのかに行き着くのですけれど、水でやる方法は、ナイロンのみならず、他のモノマーから合成された樹脂にも応用可能な技術なのです。これを皮切りに、他の樹脂にも展開できるだろうと見込んでいます。
東レさんは総合樹脂メーカーとして他の樹脂に応用できる知見や技術を持っているだろうということから、末永く共創が続けられると思い、パートナーとして決定させていただいたのです。
(富永)
ナイロン6は自動車以外にも、衣料や産業用途等、多様に使われていますが、例えば衣服ではナイロン6の裏地に違う素材のものが使われていたりして、複合化することで素材が高機能化し、より便利に、より快適になる一方で、リサイクルする際には、複合化しているがゆえに難しさが増すのです。
また自動車部品には厳しいスペックがあり、その基準を達成するために強化剤や各種添加剤を入れて安心・安全な部品にしています。そんなナイロン6をうまくリサイクルできれば、他の産業用や衣類用も含めて、リサイクルできる用途がひろがっていくのではないかというのが、私どもの考え方のひとつです。
更に、自動車にはそれぞれの機能に適した樹脂が使われます。ナイロン6がリサイクルできたからと言って、ナイロン6だけで自動車が出来るかというと、とても出来ません。ポリエステルやウレタンなど、自動車にはいろいろな樹脂が使われます。そこに共通の技術でうまくリサイクル出来れば素晴らしい成果となりますが、本当に可能かどうかは、これからのチャレンジです。
ー 今後、どのような計画で進めていくのですか?
(富永)
今後は部品処理量500トン/年規模のパイロット設備を一緒に作り、ナイロン6自動車部品が亜臨界水で連続的にリサイクル処理可能かを検証していく計画です。パイロットスケールでの連続処理を検証していく中で課題を抽出し、次のステージとなる生産実機のあるべき姿を一緒に作っていきます。
(平脇氏)
先述のように、一定の役割分担はあるものの、基本的には共創ということで一緒に知恵を出し合ってやっていくというスタンスです。プラント設備についても同様で、ホンダも一緒になって考えています。
ー 現時点での課題は?
(富永)
ホンダさんのところで、金属以外にどのような異物があるのかを見せてもらっており、サンプルも貰っています。そうした異物を含んだ状態のものを実際に亜臨界水で処理して、既存のケミカルリサイクルと同じようにきれいにモノマーに出来るのかを、ひとつずつ見ている状況です。
異物をどこまで選別・分別しなくてはいけないか。そうした基本方針を、お互いの知見を出し合いながら議論を始めています。